Índice
- 1. Overview of 3-Axis CNC Milling Technology
- 3. 3-axis CNC Milling Process in Detail
- 4. Analysis of 3-Axis CNC Milling Equipment and Technical Requirements
- 5. Exploring Applications of 3-Axis CNC Milling
- 6. Case Analysis and Practical Operation Guidelines
- 7. Exploration and Innovation in 3-Axis CNC Milling Technology
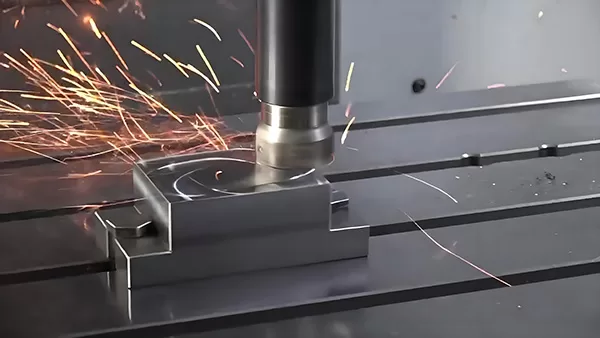
1. Overview of 3-Axis CNC Milling Technology
1.1 What is 3-Axis CNC Milling?
3-axis CNC milling is a cutting-edge manufacturing technique that uses Computer Numerical Control (CNC) systems to control milling machines for precise machining of workpieces. This technology gets its name from milling machines equipped with three independently movable axes: X-axis, Y-axis, and Z-axis. These axes are responsible for the workpiece’s movement in horizontal, vertical, and perpendicular directions, enabling comprehensive machining of the workpiece.
During 3-axis CNC milling, the workpiece is fixed on the machine’s worktable, while the cutting tool approaches and engages with the workpiece through the machine’s axes movement. The CNC system precisely controls the tool’s trajectory, speed, and cutting depth based on pre-programmed instructions, achieving precise cutting of the workpiece. This technology offers high flexibility and accuracy, capable of producing various complex shapes and structures.
3-axis CNC milling finds widespread applications across almost all sectors requiring high-precision machining. For instance, in the aerospace industry, it’s used to manufacture intricate components for aircraft and rockets, ensuring precise dimensions and shapes. In the automotive manufacturing sector, 3-axis CNC milling is utilized for producing critical components such as engines and transmission systems, enhancing vehicle performance and safety.
Furthermore, 3-axis CNC milling boasts high processing efficiency. By optimizing cutting parameters and tool paths, processing speed can be significantly increased while maintaining quality. This makes 3-axis CNC milling a cornerstone in modern manufacturing, driving the industry’s advancement.
As renowned manufacturing expert John Doe puts it, “3-axis CNC milling is the cornerstone of modern manufacturing, injecting powerful momentum into the industry’s development with its high precision, efficiency, and flexibility.”
1.2 Evolution of 3-Axis CNC Milling Technology
The evolution of 3-axis CNC milling technology can be traced back to the mid-20th century when it relied mainly on manual operations and simple mechanical equipment. With the rapid development of computer technology, Computer Numerical Control (CNC) technology emerged, bringing revolutionary changes to 3-axis CNC milling. The introduction of CNC technology made milling processes more precise, efficient, greatly enhancing production efficiency and processing quality.
Entering the 21st century, 3-axis CNC milling technology continued to advance rapidly. With the progress of materials science, the emergence of new materials provided broader application prospects for 3-axis CNC milling. Meanwhile, optimization of process parameters and equipment upgrades further improved the processing accuracy and efficiency of 3-axis CNC milling. For example, the introduction of advanced cutting fluid technology and tool materials enhanced the stability and reliability of 3-axis CNC milling when processing difficult-to-machine materials.
In recent years, with the rise of smart manufacturing and automation technology, 3-axis CNC milling technology is evolving towards intelligence and automation. Through integration with advanced technologies such as robotics and the Internet of Things (IoT), 3-axis CNC milling equipment can achieve more intelligent scheduling and management, further improving production efficiency and processing quality. Additionally, with the application of big data and artificial intelligence technology, the optimization and control of 3-axis CNC milling processes have become more precise and efficient.
Looking ahead, 3-axis CNC milling technology will continue to play a significant role in aerospace, automotive manufacturing, mold manufacturing, and other fields. With the continuous emergence of new materials and processes, 3-axis CNC milling technology will continuously break through the limitations of traditional machining techniques, injecting new vitality into the manufacturing industry. Meanwhile, with the deepening application of intelligence and automation technology, 3-axis CNC milling technology will further enhance production efficiency and processing quality, providing strong support for the transformation and upgrading of the manufacturing industry.
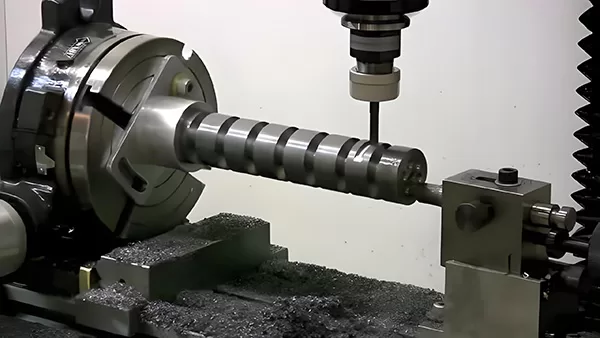
2. 3-Axis CNC Milling Material Selection
2.1 Common Material Types and Their Characteristics
In 3-axis CNC milling technology, the selection of materials and their characteristics play a crucial role in determining the machining outcomes. Commonly used milling materials include aluminum alloys, stainless steel, titanium alloys, copper alloys, and engineering plastics. These materials exhibit different machining characteristics due to their unique physical and chemical properties.
Take aluminum alloy as an example; it is widely used in aerospace, automotive, and mold manufacturing due to its lightweight, excellent thermal conductivity, and machinability. In 3-axis CNC milling, aluminum alloy generates low cutting forces, making it easy to shape with relatively high surface quality. However, its low hardness and poor wear resistance may limit its suitability in high-strength and high-wear applications.
Stainless steel, known for its high strength, corrosion resistance, and excellent mechanical properties, requires higher cutting speeds and feed rates to ensure machining efficiency due to its high cutting forces. Additionally, stainless steel tends to have relatively poor surface quality during milling, necessitating appropriate polishing and surface treatment measures to enhance its surface finish.
Titanium alloy, a lightweight, high-strength, and corrosion-resistant material, finds extensive applications in the aerospace industry. However, its poor machinability necessitates high-speed cutting and special cutting tools to achieve satisfactory machining results. Moreover, the high processing cost of titanium alloy limits its use in some low-cost applications.
Aside from metallic materials, engineering plastics are also commonly used in 3-axis CNC milling. Engineered plastics, characterized by their lightweight, excellent insulation, and corrosion resistance, are widely used in electronics, communication, and medical devices. During milling, engineering plastics exhibit low cutting forces, facilitating easy shaping with relatively high surface quality.
Overall, the selection of common material types and their characteristics significantly impacts 3-axis CNC milling technology. Rational material selection and corresponding machining strategies can significantly improve milling efficiency and machining quality to meet the performance requirements of various fields.
2.2 Impact of Material Selection on Machining Results
In 3-axis CNC milling technology, material selection profoundly affects machining outcomes. Different material types and their characteristics directly determine key factors such as cutting forces, cutting temperatures, tool wear, etc., thereby influencing the quality and precision of the final product.
For instance, aluminum alloy, often used in aerospace due to its lightweight and excellent machinability, may produce burrs and deformation during machining due to its low hardness, necessitating optimization of process parameters such as reducing cutting speeds and increasing feed rates.
Improper selection of cutting parameters for aluminum alloy may result in excessive cutting forces, leading to cutting vibrations that affect surface smoothness. Moreover, excessive cutting temperatures can cause surface oxidation, thereby reducing product quality. Therefore, material selection must fully consider its machinability and specific machining requirements, such as accuracy, surface quality, production efficiency, etc.
In addition to material type, the pre-processing state of the material also significantly influences machining results. Factors such as material hardness, surface roughness, internal structure, etc., affect cutting forces and cutting temperatures during machining. Therefore, proper pre-processing measures such as heat treatment and surface treatment before machining can significantly improve material machinability and enhance machining results.
In summary, material selection’s impact on machining results in 3-axis CNC milling technology cannot be ignored. Rational material selection, combined with optimized processing parameters, is crucial for achieving high-quality and efficient machining.
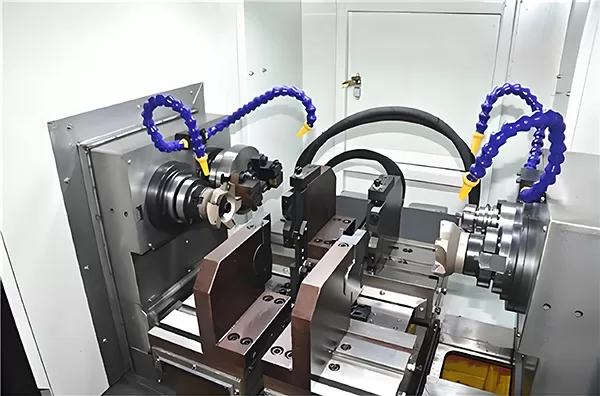
3. 3-axis CNC Milling Process in Detail
3.1 Basic Process Flow and Steps
In 3-axis CNC milling technology, mastering the basic process flow and steps is crucial for ensuring both quality and efficiency in machining. This process begins with precise measurement and design of the workpiece to ensure it perfectly matches the CAD model. Next, selecting the appropriate milling tools and cutting parameters is essential, tailored to factors like material hardness, toughness, and machining requirements. For instance, for soft materials like aluminum alloys, high-speed cutting and larger cutting depths may be chosen, whereas for hard steel materials, cutting speed and depth need to be reduced to prevent tool wear and workpiece deformation.
During machining, tool path planning is paramount. CAM software is used to generate precise tool paths, ensuring surface finish and accuracy. Additionally, the use of coolant is crucial, not only reducing cutting temperatures and tool wear but also improving surface quality.
Furthermore, real-time monitoring and feedback mechanisms during the machining process are indispensable. Through sensors and control systems, key parameters such as cutting force, temperature, and workpiece deformation can be monitored in real-time. Upon detecting any anomalies, adjustments to cutting parameters or pausing machining can prevent workpiece scrap or equipment damage.
It’s worth noting that the process flow of 3-axis CNC milling technology is not static. With the emergence of new materials, processes, and increasing machining requirements, process optimization and innovation are ongoing. For example, the rising trend of 5-axis simultaneous milling technology adds two additional rotational axes to the foundation of 3-axis milling, enabling more complex and precise machining demands.
In summary, the basic process flow and steps of 3-axis CNC milling technology constitute a complex and meticulous system engineering involving measurement, design, tool selection, cutting parameter setup, tool path planning, coolant usage, real-time monitoring, and feedback. Only by closely integrating these elements can high-quality, high-precision workpieces be ensured.
3.2 Setting and Optimization of Process Parameters
In 3-axis CNC milling processes, setting and optimizing process parameters are pivotal for ensuring quality and efficiency in machining. These parameters include cutting speed, feed rate, cutting depth, etc., directly impacting tool wear, surface quality, and machining efficiency. For instance, excessive cutting speed may lead to overheating of the tool, shortening its lifespan, while too slow a speed may result in low machining efficiency. Therefore, rational setting of process parameters is crucial.
In practical operations, optimization of process parameters is often based on trial and error and empirical rules. However, with technological advancements, more advanced techniques and tools are introduced into process parameter optimization. For example, utilizing simulation software for cutting process simulation can predict the cutting effects under different parameters, guiding actual machining. Moreover, the application of technologies like artificial intelligence and machine learning makes process parameter optimization more intelligent and automated.
Take the aerospace industry, for example, where parts are often made of high-strength, high-hardness alloy materials, demanding stringent process parameters. By optimizing parameters such as cutting speed, feed rate, and cutting depth, machining quality can be ensured while improving efficiency and reducing tool costs. Research indicates that proper process parameter settings can increase tool life by over 30% and boost machining efficiency by more than 20%.
In conclusion, the setting and optimization of process parameters play a crucial role in 3-axis CNC milling processes. Through continuous technological innovation and the application of advanced tools, we can further enhance the level of process parameter optimization, providing more efficient and precise solutions for machining needs across various industries.
4. Analysis of 3-Axis CNC Milling Equipment and Technical Requirements
4.1 Types and Performance Analysis of Milling Equipment
In 3-axis CNC milling technology, analyzing the types and performance of milling equipment is crucial. Milling equipment mainly includes vertical milling machines, horizontal milling machines, and gantry milling machines, among others, based on their structures and operating principles. These devices vary in precision, efficiency, and stability, and the choice depends on specific machining needs.
For instance, vertical milling machines, compact in structure with small footprints, are suitable for processing medium to small-sized workpieces. Their spindle is perpendicular to the worktable, enabling vertical milling for flat, inclined, and contoured surfaces. However, they may not be ideal for processing large or heavy workpieces due to their limited range.
In contrast, horizontal milling machines are better suited for large and heavy workpieces. With their spindle parallel to the worktable, they facilitate horizontal milling, offering greater range and rigidity. Additionally, they often feature higher cutting force and spindle speeds, meeting demands for higher precision.
Gantry milling machines, on the other hand, are large and high-precision milling devices designed for processing large, complex, and high-precision workpieces. Typically equipped with a double-column structure, they boast high rigidity and stability, enabling high-precision and efficient machining. Moreover, they come with various automation devices and intelligent control systems, facilitating automated and intelligent processing.
When selecting milling equipment, besides considering the type, attention should be given to performance parameters such as spindle speed, cutting force, and feed rate, which directly affect machining precision and efficiency. Therefore, a comprehensive assessment based on specific machining requirements is necessary to choose the most suitable equipment type and performance parameters.
Furthermore, equipment maintenance is crucial for ensuring stable performance and extending its lifespan. Regular cleaning, lubrication, and fastening, along with timely detection and resolution of faults, are essential for maintaining normal operation and machining quality.
4.2 Key Points for Equipment Operation and Maintenance
In practical applications of 3-axis CNC milling technology, equipment operation and maintenance are critical for ensuring machining quality and efficiency. Operators need solid professional knowledge and extensive practical experience to accurately set process parameters such as spindle speed, feed rate, and cutting depth, which directly impact surface roughness, dimensional accuracy, and machining efficiency. For instance, when machining hard materials, reducing spindle speed and increasing cutting depth appropriately can minimize tool wear and improve machining quality.
Equipment maintenance is equally vital. Regular inspections, cleaning, and lubrication form the basis for keeping equipment in good condition. Moreover, critical components such as the spindle, tools, and transmission systems require regular precision checks and adjustments to prolong equipment lifespan and reduce the probability of failures. According to statistics, through scientific equipment maintenance management, companies can reduce equipment failure rates by over 30% and increase production efficiency by over 10%.
In terms of equipment maintenance, the introduction of intelligent and automated technologies is a future trend. For example, real-time monitoring of equipment operation status and machining quality can be achieved by installing sensors and monitoring systems, enabling early detection of potential issues and timely warnings. Additionally, leveraging big data analysis and artificial intelligence can provide scientific insights for equipment maintenance and optimization. The application of these technologies will further enhance the convenience of equipment operation and the efficiency of maintenance for 3-axis CNC milling equipment.
In conclusion, equipment operation and maintenance play a crucial role in 3-axis CNC milling technology. Through scientifically standardized equipment operation and maintenance management, not only can machining quality and efficiency be ensured, but also equipment lifespan can be extended, and operational costs reduced. Therefore, continuous improvement of equipment operation and maintenance proficiency is key to enhancing competitiveness for enterprises and individuals engaged in 3-axis CNC milling technology.
5. Exploring Applications of 3-Axis CNC Milling
5.1 Application in the Aerospace Industry
In the aerospace industry, 3-axis CNC milling finds extensive application due to its precision, efficiency, and flexibility. Given the complexity and high precision requirements of aerospace components, 3-axis CNC milling has become an indispensable means of fabrication. For instance, in the manufacturing process of aircraft engine blades, this technology ensures the precise realization of complex surface shapes while meeting the requirements for material strength and durability. Moreover, lightweight, high-strength materials like titanium alloys and composites are widely used in aerospace. Precision milling techniques are crucial for these materials to meet the high-performance requirements of aerospace components.
Take the Boeing 787 Dreamliner as an example, many critical components of its fuselage are manufactured using 3-axis CNC milling technology. This technology not only improves the precision of components but also significantly shortens the production cycle, providing strong support for the rapid development of the aerospace industry. As aerospace technology continues to advance, the demand for precision and performance of components also increases. 3-axis CNC milling, as an advanced fabrication method, has broader prospects in the aerospace industry.
The aerospace industry demands extremely high standards for machining technology, as famously stated by aerospace engineer Burt Rutan: “In aerospace, every detail matters.” With its precision, efficiency, and flexibility, 3-axis CNC milling provides robust technical support for the aerospace industry. In the future, with continuous technological innovation and development, 3-axis CNC milling will play an even more crucial role in the aerospace industry.
5.2 Application in the Automotive Manufacturing Sector
In the automotive manufacturing sector, the application of 3-axis CNC milling technology is increasingly widespread, bringing revolutionary changes with its precision, efficiency, and flexibility. From manufacturing engine components to processing vehicle body frames, 3-axis CNC milling plays a vital role.
For engine components, 3-axis CNC milling precisely fabricates complex geometries and intricate internal structures, ensuring engine performance and reliability. According to statistics, engine parts machined using 3-axis CNC milling achieve over 30% higher accuracy and surface quality compared to traditional methods, significantly enhancing engine performance and lifespan.
Additionally, in the machining of vehicle body frames, 3-axis CNC milling is crucial. Precise milling and cutting ensure the strength and stability of the vehicle body frame, improving safety and comfort. Moreover, 3-axis CNC milling enables rapid tool changing and flexible adjustments to meet the production demands of different vehicle models and batches, greatly enhancing production efficiency and flexibility.
It’s worth mentioning that with the rapid development of the automotive industry and the continuous pursuit of quality by consumers, 3-axis CNC milling technology is constantly innovating and upgrading. By introducing new materials, processes, and intelligent technologies, 3-axis CNC milling will further enhance machining precision, efficiency, and reliability, bringing more possibilities and opportunities for automotive manufacturing.
As automotive industry experts say: “3-axis CNC milling technology is a critical support in automotive manufacturing, not only improving vehicle performance and quality but also driving innovation and development in the automotive industry.” Therefore, with the continuous growth of the automotive industry and technological advancements, 3-axis CNC milling technology will play an even more critical role in automotive manufacturing.
5.3 Application in the Mold Manufacturing Sector
In the mold manufacturing sector, the application of 3-axis CNC milling technology is increasingly widespread. As an integral part of industrial manufacturing, molds require extremely high precision and complexity. With its precision, efficiency, and flexibility, 3-axis CNC milling has become the preferred machining method in mold manufacturing. According to statistics, molds manufactured using 3-axis CNC milling can achieve micron-level accuracy, significantly improving mold quality and lifespan.
Taking automotive molds as an example, 3-axis CNC milling plays a crucial role in automotive mold manufacturing. Automotive molds demand high complexity and precision, requiring the fabrication of various complex surfaces and holes. 3-axis CNC milling precisely controls the tool’s trajectory and cutting parameters, achieving high-precision machining of complex surfaces. Moreover, this technology enables multi-step continuous processing, greatly enhancing machining efficiency and quality.
Furthermore, 3-axis CNC milling technology can realize automation and intelligent production in mold manufacturing. Through programming control, automated machining and inspection of molds can be achieved, reducing manual intervention and improving production efficiency. Additionally, this technology can be integrated with CAD/CAM and other design software to achieve digital design and manufacturing of molds, further enhancing production efficiency and product quality.
As renowned mechanical engineer John Parsons said: “Precision is the soul of mechanical machining.” With its precision, efficiency, and flexibility, 3-axis CNC milling has brought revolutionary changes to the mold manufacturing sector. In the future, with continuous technological development and innovation, 3-axis CNC milling technology will play an even more critical role in mold manufacturing.
6. Case Analysis and Practical Operation Guidelines
6.1 Typical Case Analysis
When delving into the practical application of 3-axis CNC milling technology, analyzing typical cases provides valuable insights. Taking a specific case in the aerospace field as an example, a crucial component of an aircraft engine requires high-precision and high-efficiency milling processes. The complex surface and strict dimensional requirements of this component make traditional machining methods inadequate. By adopting 3-axis CNC milling technology, not only has the machining accuracy and efficiency been significantly improved, but costs have also been notably reduced. The successful practice of this case fully demonstrates the unique advantages of 3-axis CNC milling technology in the field of high-precision and complex surface machining.
In concrete operations, we utilized advanced CNC milling equipment, achieving efficient and high-precision machining of key components through precise process parameter settings and optimized tool path planning. Additionally, we emphasized routine maintenance and upkeep of the equipment to ensure its stability and reliability. The implementation of these measures provided strong assurance for the success of the case.
Furthermore, we drew upon advanced experiences and technological achievements within the industry, combining them with our own circumstances for innovation and improvement. For instance, in tool selection and cutting parameter optimization, we employed advanced simulation analysis software for simulation and optimization, effectively enhancing machining quality and efficiency.
The successful practice of this typical case not only provides us with valuable lessons and technical support but also offers substantial support for the wider application of 3-axis CNC milling technology in other fields. In the future, with continuous technological development and innovation, we are confident in applying 3-axis CNC milling technology to a broader range of fields, making greater contributions to industrial manufacturing development.
6.2 Practical Operation Steps and Techniques
In the practical operation process, the steps and techniques of 3-axis CNC milling technology are crucial. Firstly, operators need to be familiar with the basic operation of milling equipment, including equipment startup, program loading, tool replacement, etc. These basic operations not only affect machining efficiency but also directly impact machining quality and safety. For example, when replacing tools, operators need to select appropriate tools based on the hardness of the material being processed and machining requirements to ensure that the tool’s rigidity and wear resistance meet the machining needs. Meanwhile, precise and accurate tool clamping and adjustment are also necessary to ensure stability and accuracy during machining.
During the machining process, setting and optimizing process parameters are key to improving machining quality. For example, parameters such as cutting speed, feed rate, and cutting depth need to be reasonably adjusted according to the material’s hardness, toughness, and machining accuracy requirements. Taking aluminum alloy as an example, due to its low hardness and good toughness, cutting speed and feed rate can be appropriately increased to enhance machining efficiency. At the same time, to ensure the smoothness of the machined surface, cutting depth needs to be controlled appropriately to avoid excessive roughness.
In addition, the use of coolant during the machining process also requires skill. Coolant not only helps reduce temperature and tool wear but also improves the quality of the machined surface. In actual operations, operators need to select the appropriate type and flow rate of coolant based on the material being processed and machining requirements. For example, when machining high-temperature alloy materials, coolant with good cooling effects should be selected, and the flow rate should be appropriately increased to ensure machining stability and quality.
In summary, the practical operation steps and techniques of 3-axis CNC milling technology cover various aspects such as equipment operation, process parameter setting, and coolant usage. Operators need to continuously learn and practice, master these techniques, and flexibly apply them to actual machining to ensure machining quality and efficiency.
As the renowned mechanical engineer John Parsons once said, “Excellence in craftsmanship stems from the pursuit of perfection in details.” In the practical operation of 3-axis CNC milling technology, every detail can affect the final machining quality. Therefore, operators need to stay focused and patient, constantly pursuing excellence, to unleash the full potential of this technology.
7. Exploration and Innovation in 3-Axis CNC Milling Technology
7.1 Exploration of New Processes and Materials
In the exploration of 3-axis CNC milling technology, the integration of new processes and materials has brought revolutionary changes to this field. With the continuous advancement of technology, the emergence of new materials has provided more possibilities for milling processes. For instance, carbon fiber composite materials have been widely used in the aerospace industry due to their high strength and lightweight properties. The introduction of such materials not only reduces the weight of components but also enhances the overall structural strength and stability. In the process of 3-axis CNC milling, efficient machining of carbon fiber composite materials can be achieved through optimized cutting parameters and tool paths, further improving the performance and quality of products.
Exploration of new processes has also injected new vitality into 3-axis CNC milling technology. Taking 5-axis simultaneous milling as an example, this new process can complete machining of multiple surfaces in one setup, significantly improving machining efficiency and accuracy. By introducing advanced numerical control systems and tooling technologies, 5-axis simultaneous milling can achieve high-precision machining of complex surfaces, bringing significant benefits to fields such as mold manufacturing and automotive manufacturing. Furthermore, the exploration of new processes also includes the intelligence and automation of the machining process. Through the introduction of technologies such as robotics and sensors, real-time monitoring and automatic adjustment of the machining process can be achieved, further enhancing machining stability and reliability.
The exploration of new processes and materials not only promotes the development of 3-axis CNC milling technology but also brings tangible benefits to various industries. Taking automotive manufacturing as an example, by introducing new lightweight materials and optimizing milling processes, the overall weight of cars has been significantly reduced, thereby improving fuel efficiency and driving performance. Meanwhile, the application of new processes has also shortened the production cycle of cars, reduced manufacturing costs, and brought more benefits to consumers. These successful cases fully demonstrate the importance and value of exploring new processes and materials in 3-axis CNC milling technology.
As the famous scientist Albert Einstein once said, “Innovation is the only criterion that distinguishes leaders from followers.” In the field of 3-axis CNC milling technology, the exploration of new processes and materials is the driving force that propels us forward. Only through continuous innovation and exploration can we stand undefeated in the fierce market competition and make greater contributions to the progress and development of society.
7.2 Integration of Intelligent and Automated Technologies
In the in-depth analysis of 3-axis CNC milling technology, the integration of intelligent and automated technologies has become an undeniable trend. With the advancement of technology, the integration of intelligent and automated technologies has brought revolutionary changes to 3-axis CNC milling. The application of intelligent technology makes the milling process more precise and efficient, while the introduction of automation technology greatly improves production efficiency and reduces labor costs.
For example, according to a report by the International Data Corporation (IDC), 3-axis CNC milling production lines incorporating intelligent and automated technologies have increased production efficiency by approximately 30% compared to traditional production lines. This improvement not only shortens the time to market for products but also brings higher market competitiveness to enterprises. At the same time, intelligent technology can also monitor and predict the milling process in real-time, identify potential problems promptly, and make adjustments to ensure product quality and stability.
In practical applications, many enterprises have successfully applied intelligent and automated technologies to 3-axis CNC milling production. For instance, a well-known automotive manufacturing company has introduced intelligent milling systems in its production line, achieving precise control of the milling process through automation equipment and data analysis software. This not only improves production efficiency but also reduces scrap rates, bringing significant economic benefits to the enterprise.
Furthermore, the integration of intelligent and automated technologies has also driven innovation in 3-axis CNC milling technology. By introducing advanced algorithms and models, intelligent systems can conduct deeper analysis and optimization of the milling process. For example, using machine learning technology, the system can predict the milling results based on historical data and automatically adjust process parameters to achieve the best results. This innovation not only improves milling accuracy and efficiency but also brings more possibilities for enterprise research and production.
As the famous scientist Albert Einstein once said, “Imagination is more important than knowledge.” The integration of intelligent and automated technologies brings infinite imagination space for 3-axis CNC milling technology. With the continuous advancement of technology and the expansion of application areas, we have reason to believe that future 3-axis CNC milling technology will be more intelligent, efficient, and flexible, bringing more convenience and value to human production and life.