Rapid Prototyping For Automotive Industry Solution

In today’s fast-paced automotive industry, staying ahead of the competition and delivering cutting-edge solutions is crucial. Rapid prototyping has emerged as a game-changer, revolutionizing the way automotive products are developed, designed, and manufactured. By leveraging advanced technologies and techniques, rapid prototyping offers numerous benefits that enhance the automotive industry’s efficiency, innovation, and profitability. This article explores the diverse facets of Automotive Industry solution, delving into its benefits, techniques, applications, case studies, best practices, future trends, choosing the right service provider, and addressing common queries.
Benefits of Rapid Prototyping for Automotive Industry:
1. Improved Product Development Process:
Rapid prototyping significantly accelerates the product development process, enabling faster iterations and reducing time-to-market. It allows automotive manufacturers to swiftly transform ideas into tangible prototypes, facilitating quick design validation and enhancing overall product quality.
2. Accelerated Time-to-Market:
By streamlining the development cycle, rapid prototyping expedites the time-to-market for automotive products. It minimizes the delays associated with traditional manufacturing methods, empowering manufacturers to respond quickly to market demands and gain a competitive edge.
3. Enhanced Design Flexibility:
Rapid prototyping offers unparalleled design flexibility, allowing automotive designers and engineers to explore creative concepts and make on-the-fly modifications. This flexibility fosters innovation, encourages experimentation, and leads to more refined and optimized designs.
3. Cost Savings in Production:
Through rapid prototyping, automotive manufacturers can identify and address design flaws and manufacturing issues at an early stage, reducing costly errors during mass production. The ability to detect and rectify problems upfront ultimately saves significant production costs.
Rapid Prototyping Techniques in the Automotive Industry:
1. 3D Printing for Automotive Prototypes:
Utilizing additive manufacturing technology, 3D printing enables the creation of complex automotive prototypes with exceptional precision and detail. It offers the flexibility to produce intricate geometries, functional parts, and even full-scale concept models, providing invaluable insights during the design and validation stages.
2. CNC Machining for Rapid Tooling:
CNC machining plays a vital role in rapid tooling for automotive parts production. It allows for the quick and accurate fabrication of molds, dies, and other tooling components required for mass production. CNC machining ensures high-quality tooling, minimizing errors and optimizing the manufacturing process.
3. Vacuum Casting for Small Batch Production:
Vacuum casting is a valuable technique for small batch production in the automotive industry. It enables the replication of functional prototypes and end-use parts using a wide range of materials. Vacuum casting provides a cost-effective solution for producing low-volume components with excellent surface finish and mechanical properties.
4. Laser Cutting and Engraving for Custom Components:
Laser cutting and engraving technologies offer precise and efficient methods for creating custom automotive components. They are particularly useful for fabricating interior and exterior trim pieces, signage, labeling, and other personalized elements. Laser-based techniques ensure high accuracy, intricate detailing, and consistent quality.
Applications of Rapid Prototyping in the Automotive Industry:
1. Concept Car Design and Development:
Rapid prototyping has transformed the concept car design and development process. It enables designers to bring their visionary ideas to life by creating physical prototypes that showcase futuristic designs, novel features, and advanced technologies. Concept cars serve as powerful marketing tools and drive innovation in the automotive industry.
2. Functional Prototypes for Testing and Validation:
Rapid prototyping allows automotive manufacturers to produce functional prototypes that accurately simulate the performance and behavior of final products. These prototypes undergo rigorous testing and validation, enabling engineers to identify and rectify design flaws, optimize functionality, and enhance overall product performance.
3. Customized Automotive Parts Production:
The automotive industry is witnessing a shift towards customization, and rapid prototyping plays a vital role in producing customized automotive parts. From personalized interior components to bespoke exterior features, rapid prototyping offers the means to create one-of-a-kind elements that meet specific customer requirements.
4. Interior and Exterior Trim Components:
Rapid prototyping technologies empower automotive designers to create intricate interior and exterior trim components with exceptional aesthetics and functionality. From dashboard panels and center console elements to intricate grilles and lighting assemblies, rapid prototyping ensures precise fitment, seamless integration, and stunning visual appeal.
Case Studies: Successful Implementation of Rapid Prototyping in the Automotive Industry:
1. BYD Motors: Reducing Time and Costs with 3D Printed Prototypes:
BYD Motors successfully implemented rapid prototyping using 3D printing technology, enabling them to significantly reduce the time and costs associated with prototype development. By leveraging the speed and accuracy of 3D printing, they streamlined their design iterations, optimized product performance, and gained a competitive advantage in the market.
2. Volkswagen Automotive: Improving Design Iterations with CNC Machining:
Volkswagen Automotive utilized CNC machining for rapid tooling, revolutionizing their design iteration process. By quickly fabricating precise molds and tooling components, they were able to expedite their development timeline, enhance design accuracy, and efficiently transition to mass production, resulting in improved product quality and reduced time-to-market.
3. Toyota Car Manufacturing: Streamlining Production with Vacuum Casting:
Toyota Car Manufacturing implemented vacuum casting for small batch production, revolutionizing their manufacturing process. By utilizing the flexibility and cost-effectiveness of vacuum casting, they successfully produced low-volume automotive parts with excellent surface finish and mechanical properties, ultimately reducing production costs and increasing customer satisfaction.
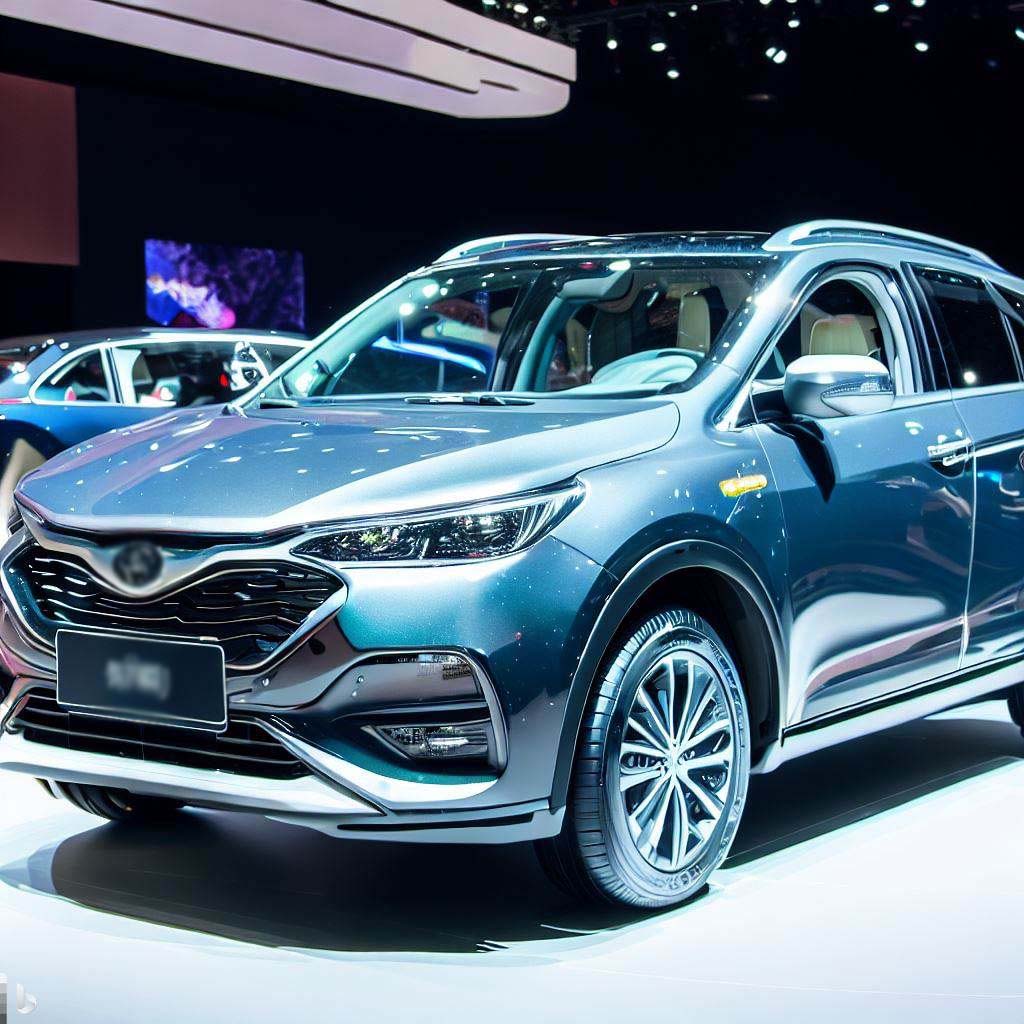


Best Practices for Implementing Rapid Prototyping in the Automotive Industry:
1. Collaborative Design Processes:
Effective collaboration between designers, engineers, and manufacturers is essential for successful rapid prototyping implementation. Foster open communication, shared goals, and cross-functional teamwork to maximize the benefits of rapid prototyping throughout the automotive product development cycle.
2. Material Selection for Automotive Applications:
Carefully choose materials suitable for automotive applications to ensure optimal performance, durability, and safety. Consider factors such as mechanical properties, heat resistance, chemical compatibility, and regulatory compliance when selecting materials for rapid prototyping in the automotive industry.
3. Quality Control and Testing Standards:
Establish stringent quality control measures and adhere to industry-specific testing standards throughout the rapid prototyping process. Regularly monitor and evaluate the quality of prototypes and final products to maintain consistency, reliability, and compliance with industry regulations.
4. Integration with Traditional Manufacturing Methods:
While rapid prototyping offers numerous advantages, it is crucial to integrate it seamlessly with traditional manufacturing methods. Evaluate the feasibility of scaling up production, optimizing efficiency, and achieving cost-effectiveness when transitioning from prototyping to mass manufacturing.
Future Trends in Rapid Prototyping for the Automotive Industry:
1. Advancements in Materials and Printing Technologies:
Continuous advancements in materials science and printing technologies will unlock new possibilities in rapid prototyping for the automotive industry. Materials with enhanced strength, durability, and thermal properties, combined with faster and more precise printing techniques, will revolutionize the production of automotive components.
2. Integration of Artificial Intelligence in Design Optimization:
Artificial intelligence (AI) will play a significant role in optimizing design processes and enhancing automotive product performance. AI algorithms will assist in generative design, topology optimization, and simulation-based analysis, enabling the creation of lightweight, efficient, and innovative automotive designs.
3. On-Demand Manufacturing and Localized Production:
The concept of on-demand manufacturing and localized production will gain prominence in the automotive industry. Rapid prototyping technologies, combined with efficient supply chain management, will enable customized automotive part production near the point of demand, reducing lead times, inventory costs, and environmental impact.
Choosing a Rapid Prototyping Service Provider for the Automotive Industry:
1. Factors to Consider When Selecting a Provider:
When choosing a rapid prototyping service provider, consider factors such as expertise, experience, technological capabilities, and track record. Assess their ability to meet your specific automotive industry requirements and deliver high-quality prototypes within the desired timeframe.
2. Evaluating Experience and Expertise:
Evaluate the provider’s experience in the automotive industry and their expertise in utilizing rapid prototyping technologies. Look for case studies, client testimonials, and references to gauge their success in delivering automotive prototypes that meet quality standards and design specifications.
3. Assessing Quality Control Measures:
Quality control is crucial in rapid prototyping. Assess the provider’s quality control measures, certifications, and adherence to industry standards. Ensure that they have robust processes in place to guarantee the accuracy, functionality, and reliability of the prototypes they produce.
4. Reviewing Client Testimonials and Portfolio:
Review client testimonials and examine the provider’s portfolio to gauge the breadth and depth of their experience in the automotive industry. Look for evidence of successful projects, diverse capabilities, and the ability to handle complex automotive prototyping challenges.
Frequently Asked Questions about Rapid Prototyping for the Automotive Industry:
1. What is the typical turnaround time for a rapid prototyping project?
The turnaround time for a rapid prototyping project varies depending on the complexity of the design, chosen technology, and the provider’s workload. However, rapid prototyping significantly reduces development timelines compared to traditional manufacturing methods, with some projects completed within days or weeks.
2. Can rapid prototyping be used for large-scale production?
While rapid prototyping is primarily used for prototyping and small batch production, it can be integrated into large-scale production processes. However, factors such as cost, production speed, and material suitability need careful consideration to determine the feasibility of using rapid prototyping for mass manufacturing.
3. What are the cost implications of implementing rapid prototyping?
The cost implications of implementing rapid prototyping depend on various factors, including project complexity, material selection, chosen technology, and quantity of prototypes. Rapid prototyping can offer cost savings by reducing design iterations, minimizing production errors, and accelerating time-to-market, ultimately enhancing overall cost-efficiency.
4. How does rapid prototyping contribute to innovation in the automotive sector?
Rapid prototyping fosters innovation in the automotive sector by facilitating the exploration of new design concepts, enabling quick iteration and validation, and promoting collaboration between designers, engineers, and manufacturers. It accelerates the innovation cycle, encourages experimentation, and drives the development of advanced automotive solutions.
Conclusion:
Rapid prototyping has revolutionized the automotive industry, providing a wide array of benefits, including improved product development processes, accelerated time-to-market, enhanced design flexibility, and cost savings in production. By utilizing techniques such as 3D printing, CNC machining, vacuum casting, and laser cutting, automotive manufacturers can unlock new possibilities in concept car design, functional prototyping, customized part production, and trim component fabrication. Case studies highlight the successful implementation of rapid prototyping by industry leaders, and best practices ensure optimal results. With future trends including advancements in materials, AI integration, and on-demand manufacturing, the automotive industry is poised for further innovation and efficiency. By choosing the right rapid prototyping service provider and addressing common queries, automotive manufacturers can harness the full potential of rapid prototyping and drive their success in this dynamic industry.