Table of Contents
1. Overview of Mold Making Industry in China
1.1 Industry Background and Development
The development of mold making industry in China is closely linked with the process of industrialization. Since the reform and opening-up in the 1980s, the rapid development of this industry has been driven by the introduction of foreign investment and technology. Initially, it relied heavily on imported molds and imitation of technology, but gradually formed its own technical system and innovation capabilities. Entering the 21st century, with the booming development of industries such as automotive, electronics, and home appliances, the demand for molds has rapidly increased. In recent years, the Chinese mold market has continued to expand, with an annual growth rate of over 10%. In the high-end mold field, Chinese enterprises have significantly improved their technological level and product quality, gradually breaking the international monopoly. Some leading companies have not only led the domestic market through technological innovation, quality improvement, and market expansion but also successfully entered the international market. Looking ahead, the mold making industry in China will face new opportunities and challenges, requiring continuous innovation, quality improvement, and market expansion to cope with future challenges. As Joseph Schumpeter said, innovation is the fundamental driving force for economic development, and the mold making industry in China must adhere to the strategy of innovation-driven development.
1.2 Current Industry Scale and Main Production Areas
In recent years, the mold making industry in China has steadily developed, and the market scale has gradually expanded, with a total output value exceeding hundreds of billions of yuan, becoming an important part of the global mold market. This growth is mainly due to the rapid progress of China’s manufacturing industry, especially the sustained strong demand in industries such as automotive, electronics, and home appliances, providing broad market space for mold making.
While the industry scale continues to expand, the main production areas of mold making in China have gradually formed, with Guangdong, Zhejiang, Jiangsu, and other regions becoming important bases for mold making. These regions, with advanced mold technology and equipment, have attracted a large number of mold manufacturing enterprises, forming a complete industrial chain. Especially in Guangdong Province, both the output and export volume of molds rank among the top in the country, earning it the reputation of “the hometown of Chinese molds.”
The rise of these main production areas not only promotes the clustered development of the mold making industry in China but also drives technological innovation and industrial upgrading. Enterprises in these regions continuously enhance their competitiveness through methods such as introducing advanced foreign technology, strengthening independent research and development, and improving product quality, injecting new vitality into the development of the mold making industry in China.
1.3 Industry Position in the Global Market
The mold making industry in China occupies an important position in the global market, with continuous growth in export volume in recent years, benefiting from advantages in technology, scale, cost, and service. Chinese mold enterprises provide high-quality mold products to the global industry with advanced equipment, processes, and quality control, with automotive molds becoming one of the major supply sources. In addition, Chinese mold manufacturing enterprises have made significant achievements in technological innovation, such as using advanced CAD/CAM/CAE systems for mold design and applying advanced technologies such as high-speed machining and precision measurement to improve manufacturing accuracy and efficiency. Their global position is also reflected in their extensive capability for industrial chain integration, enabling them to quickly respond to market demands and provide comprehensive solutions. This capability allows Chinese molds to occupy a favorable position in global competition. Industry experts have stated that the rise of the mold making industry in China has driven the development of China’s manufacturing industry and injected new vitality into the global mold market. In the future, the position of the mold making industry in China in the global market will be more stable.

2. Chinese Mold Making Technology
2.1 Main Technical Processes of Mold Making
China’s mold making industry, after decades of development, has established a complete technical process, including design, material selection, processing, assembly, and debugging. In the design phase, software like CAD is used for precise mold design based on product requirements. Material selection is crucial for mold quality and lifespan, commonly using steel, aluminum alloy, etc. Processing involves techniques like milling and turning to ensure precision and surface quality. Assembly and debugging are the final stages, ensuring the molds meet production requirements through rigorous testing.
In recent years, technological advancements and changing market demands have driven continuous innovation in Chinese mold making. CNC machining improves precision and efficiency, while 3D printing provides new solutions for rapid manufacturing. These innovations enhance the level of Chinese mold making, bolstering global competitiveness.
However, Chinese mold making still faces challenges in certain aspects, such as dependence on imported high-end mold technology and equipment, and the need to improve independent innovation capabilities. Therefore, there is a need to strengthen technology research and development and talent cultivation to promote continuous progress.
Li Daokui emphasized that molds are at the core of manufacturing, with technology levels determining product quality and competitiveness. It’s essential to prioritize the development and innovation of mold making technology to support the transformation and upgrading of China’s manufacturing industry.
In conclusion, while the Chinese mold making industry has achieved success in technical processes, innovation, and market demand, it still faces challenges. Continuous innovation and improvement are necessary to maintain competitiveness in the global market.
2.2 Innovation and Breakthroughs in Chinese Mold Making Technology
In recent years, significant progress has been made in China’s mold making technology in digitization, intelligence, and high precision. Digital technologies such as CAD/CAM/CAE design software make mold design more precise and efficient. 3D printing technology has also shortened mold manufacturing cycles and reduced costs. With the rise of the new energy vehicle market, Chinese mold making enterprises have introduced advanced equipment and technology to improve mold precision and stability to meet high demands. In terms of technological innovation, Chinese mold making enterprises are exploring the application of advanced technologies such as artificial intelligence and big data to improve manufacturing accuracy and efficiency, contributing new ideas to the global mold manufacturing industry. The innovation and breakthroughs in Chinese mold making technology embody the principle that “innovation is the primary survival strategy” and are gradually moving towards the center stage of the world, contributing Chinese wisdom and strength to the global mold manufacturing industry.
2.3 Advantages and Challenges of Chinese Mold Making Technology
Chinese mold making technology holds significant advantages in the global market. China’s mold output accounts for over 50% of the global total, forming a vast industrial scale, which brings advantages in economies of scale and industrial chain integration. Meanwhile, the industry has made breakthroughs in innovation by introducing new technologies, processes, and materials to improve mold precision, lifespan, and reliability. The industry also emphasizes alignment with international standards, participating in international competition and cooperation to enhance technological levels and international competitiveness.
However, Chinese mold making technology also faces some challenges. Overall technical levels vary, with some enterprises lacking core technology and innovation capabilities. There is still a gap compared to international advanced levels in the high-end market, such as the manufacturing capability of high-precision, high-complexity molds and the application of new materials. Additionally, talent shortages and environmental pressures are also issues the industry needs to address.
To enhance advantages and address shortcomings, the industry needs to take multiple measures. Firstly, strengthening technology research and development and innovation is crucial, enhancing core competitiveness by introducing advanced technology, cultivating innovative talents, and increasing research and development investment. Secondly, promoting industrial upgrading and transformation, optimizing industrial structure, improving product quality, expanding the high-end market, and enhancing overall levels and international competitiveness. Meanwhile, strengthening talent cultivation and introduction, improving training systems, enhancing training quality, attracting outstanding international talents, and providing talent support for the industry.
In summary, Chinese mold making technology has significant advantages and enormous potential in the global market but still needs improvement and enhancement. Through measures such as strengthening technology research and development and innovation, promoting industrial upgrading and transformation, and strengthening talent cultivation and introduction, the Chinese mold making industry will continuously improve its technological level and international competitiveness, making greater contributions to the global mold manufacturing industry.
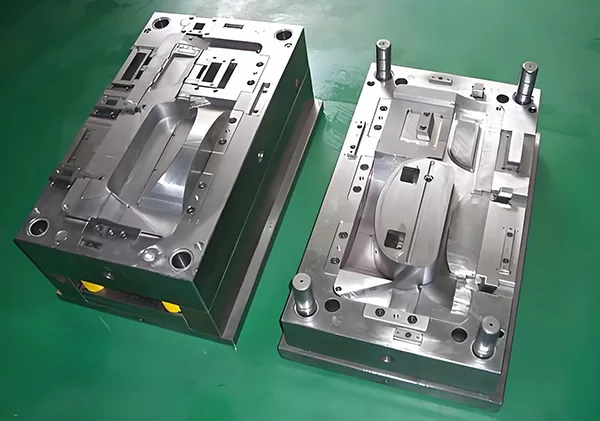
3. Applications of Mold Making in China
3.1 Mold Design and Manufacturing for Automotive Components
In the realm of automotive parts, China holds a significant position in mold making globally. Given the high complexity and precision demands of automotive parts, mold design and manufacturing require advanced technology and extensive experience. In China, mold design has evolved into a comprehensive industry chain, undergoing multiple rounds of optimization and validation from conceptual design to 3D modeling. Designers employ advanced software to analyze mold structures, materials, and processes to ensure stability and reliability.
Take the mold for automotive engine cylinder blocks as an example, where considerations include dimensional accuracy, surface roughness, and thermal stability. Precise calculations and simulations determine the critical parts of the mold design. Such molds ensure high precision and surface quality in actual production, thereby enhancing engine performance.
The mold making industry in China boasts a complete supply chain covering raw material procurement, processing, and assembly. The application of high-precision processing equipment has enhanced the precision and efficiency of mold manufacturing. Furthermore, enterprises prioritize technological innovation and process improvement to elevate manufacturing standards and quality.
Chinese mold making enterprises actively introduce international advanced technology and management experience and engage in extensive exchanges with international partners. This open and innovative approach enables the Chinese mold making industry to maintain competitiveness globally.
In conclusion, the mold making industry in China holds distinct advantages and strengths in the automotive components sector. Through technological innovation and process improvement, it will continue to make significant contributions to the global automotive industry.
3.2 Mold Applications in Electronic Product Casings and Components
Mold applications in electronic products, especially in the manufacturing of casings and components, are widespread. With technological advancements and increasing consumer demands, mold making faces greater challenges. The quality of mold design and manufacturing directly influences product appearance, performance, and market competitiveness.
For instance, in the case of smartphones, mold design must consider product structure, materials, and production processes. Mold precision and durability impact the appearance quality and user experience of smartphones. Therefore, mold manufacturers need to enhance their technical capabilities and adopt advanced equipment and processes to ensure mold precision and stability.
Data analysis and quality control are crucial in mold making. Real-time monitoring and analysis of production data enable timely problem detection and corrective actions to ensure product quality. Meanwhile, establishing and implementing a quality control system ensures that every detail of the mold meets design requirements, producing high-quality products.
New materials and technologies bring innovation pressure to mold making. The use of lightweight materials such as aluminum alloys and magnesium alloys can reduce product weight, enhancing portability. Advanced surface treatment technologies such as spraying and electroplating can enhance product appearance and durability. These innovations improve product performance and quality, bringing new opportunities to mold making.
To sum up, mold applications in electronic product casings and components are crucial parts of mold making. Facing technological progress and market changes, mold manufacturers need to continuously innovate and enhance technical capabilities to meet consumer demands. Strict quality control and innovative applications are key to ensuring mold quality and competitiveness.
3.3 Demand and Trends in Household Appliance Mold
In the midst of the transformation in the household appliance industry, the demand and trends in molds have garnered significant attention. Currently, the household appliance mold market exhibits the following characteristics:
Firstly, the growth of personalized and customized demands has become a significant market trend. Consumers have diverse requirements for the appearance, functions, and performance of household appliances, necessitating mold manufacturers to provide flexible and personalized design solutions. New types of household appliances such as smart refrigerators and multifunctional ovens pose higher precision and complexity requirements for molds.
Secondly, environmental protection and energy efficiency have become crucial development directions in the market. With the increasing global environmental awareness, consumers’ demand for energy-efficient and environmentally friendly household appliances has risen. Mold manufacturers need to focus on using environmentally friendly materials and energy-saving technologies to reduce product energy consumption and environmental impact.
Moreover, the application of smart and internet technologies brings new development opportunities to the market. By integrating intelligent technologies, household appliances can achieve functions such as remote control and smart diagnostics, enhancing product value and competitiveness. The application of internet technologies also provides convenient marketing and sales channels for mold manufacturers.
In the coming years, the household appliance mold market will continue to grow steadily. With the increasing consumer demands for quality and appearance and the application of new technologies such as smart and environmentally friendly technologies, mold manufacturers need to innovate and enhance technical capabilities to meet market changes and consumer demands. At the same time, emphasizing the application of environmental protection and energy-saving technologies contributes to the sustainable development of the household appliance industry.
In conclusion, the demand and trends in the household appliance mold market exhibit characteristics of personalization, environmental friendliness, and smartness. Mold manufacturers need to keep pace with market trends, continuously innovate, and enhance technical capabilities to meet market changes and consumer demands, thereby driving the sustainable development of the industry.
3.4 Mold Applications in the Medical Equipment and Biotechnology Field
The widespread application of molds in the medical equipment and biotechnology fields serves as a significant force driving industry innovation. The growing demand for high-precision, high-quality medical equipment presents significant market opportunities for mold manufacturing. Bioreactors are crucial equipment in biotechnology, where mold precision and stability are essential for performance and lifespan. Therefore, mold manufacturing must utilize advanced equipment and processes to ensure precision and stability.
In the medical equipment field, molds directly impact the quality and performance of high-precision products such as pacemakers and artificial joints. Mold manufacturers need to enhance their technology and introduce advanced equipment to meet industry demands. As the industry develops, mold manufacturing requirements increase, and enterprises must keep up with trends, strengthen technological innovation and product research and development to improve mold precision, stability, and reliability, meeting market changes.
In summary, mold applications in the medical equipment and biotechnology fields drive industry innovation. Manufacturing enterprises need to continuously improve technology and service quality, contributing to industry development.
3.5 Mold Innovation in Advanced Manufacturing and New Energy Fields
Mold innovation is crucial in advanced manufacturing and new energy fields. With technological advancements, Chinese mold manufacturing factories actively engage in technological innovation to maintain a leading position. In the field of new energy vehicles, molds are critical for manufacturing key components. Chinese factories have introduced advanced equipment and software to improve mold precision and efficiency while exploring the application of new materials.
In advanced manufacturing, Chinese factories integrate digital and intelligent technologies into mold design and manufacturing, using 3D printing and IoT technology to enhance efficiency and quality. Chinese factories prioritize market demand, closely cooperating with downstream enterprises to maintain competitiveness. As a renowned entrepreneur once said, innovation is the primary driving force for development. In the future, Chinese mold manufacturing factories will continue to innovate, contributing to the development of advanced manufacturing and new energy fields.
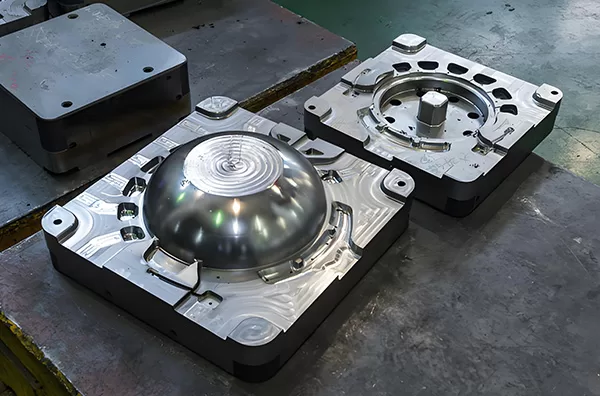
4. How to Choose the Right Mold Making Factory in China
4.1 Assessing the Technical Strength and Equipment Level of the Factory
When evaluating a mold making factory in China, it’s crucial to focus on their technical team and R&D capabilities. Excellent factories should have experienced, technically adept R&D teams that stay abreast of industry trends for continuous innovation. Additionally, the level of equipment is paramount, including advanced CNC machines, high-precision measuring instruments, and automated production lines to ensure precision and efficiency in mold making.
Take, for example, a well-known factory that has introduced internationally advanced five-axis CNC machines, enhancing both precision and efficiency in mold processing. Furthermore, the factory is equipped with sophisticated mold inspection devices and software, ensuring that the produced molds meet customer requirements and industry standards. These advantages have garnered customer trust and provided a competitive edge in the market.
Assessment should also focus on quality management systems and after-sales service. Excellent factories should have rigorous quality management systems to ensure that production processes meet standards and customer requirements. Additionally, a comprehensive after-sales service system can provide timely and professional technical support and services to customers.
In summary, evaluating the technical strength and equipment level of mold making factories in China requires considering multiple aspects comprehensively. Only through a comprehensive and objective assessment can one select a factory that truly meets their needs and provides assurance for the long-term development of their enterprise.
4.2 Understanding the Production Capacity and Quality Control of the Factory
When choosing a suitable mold making factory in China, understanding the factory’s production capacity and quality control is paramount. Production capacity not only affects whether the factory can deliver high-quality products on time but also reflects its technical strength and equipment level. Quality control directly determines the stability and reliability of products and is a key factor for customers when choosing partners.
When evaluating a factory’s production capacity, one can focus on its equipment configuration and process flow. For instance, advanced CNC machines and precision measuring equipment can ensure the accuracy and efficiency of mold making. Moreover, whether the factory employs automated production lines and intelligent management systems is also an important indicator of its level of modernization. By understanding this information, one can have a comprehensive understanding of the factory’s production capacity.
Regarding quality control, it’s crucial for factories to establish sound quality management systems and inspection methods. For example, whether the factory has obtained international quality management system certifications like ISO 9001, and whether it has professional quality inspection teams and advanced inspection equipment, are key factors in assessing its quality control capabilities. Additionally, the factory’s historical product quality records and customer feedback are important criteria for evaluating its quality stability.
Take a well-known mold making factory as an example. The factory has introduced internationally advanced production equipment and management systems, ensuring the precision and stability of every product through strict quality control processes. Its molds have been widely used in various fields such as automotive parts and electronics, earning trust and praise from numerous customers. This fully demonstrates the importance of production capacity and quality control in the mold making industry.
In summary, understanding the production capacity and quality control of the factory is crucial for choosing a suitable mold making factory in China. By thoroughly understanding and evaluating these aspects of information, one can select partners with strong technical capabilities and stable quality, laying a solid foundation for the successful implementation of projects.
4.3 Evaluating the Service Level and After-Sales Support of the Factory
When evaluating mold making factories in China, service level and after-sales support are important considerations. Excellent factories should have advanced technology, high-quality products, and excellent service. When assessing the service level, focus on professional customer service teams and customized services. Comprehensive after-sales support, including warranty, maintenance, technical support, and a well-established customer feedback mechanism, is also crucial.
Take a well-known mold making factory as an example. They have professional teams, comprehensive systems, and advanced customer relationship management systems, enabling digital and intelligent services. They respond quickly to customer needs, provide personalized solutions, and regularly collect and analyze customer feedback data to optimize product and service quality.
As Peter Drucker said, “The aim of marketing is to know and understand the customer so well the product or service fits him and sells itself.” Therefore, when evaluating mold making factories in China, in addition to focusing on technology and product quality, attention should also be paid to service level and after-sales support. Only factories that provide excellent service and comprehensive after-sales support can stand out in competition, winning customer trust and loyalty.
5. Appendix
5.1 Standards and Regulations in the Chinese Mold Making Industry
The standards and regulations in the Chinese mold making industry serve as the cornerstone for its healthy and orderly development, covering various aspects such as design, manufacturing, and inspection. These standards specify specific technical requirements for different types of molds. For instance, automotive mold standards define parameters like dimensional accuracy, surface quality, and lifespan to ensure meeting high standards in automotive manufacturing.
In recent years, with technological advancements and market developments, these standards are continually updated and enhanced, incorporating environmental requirements such as waste disposal and energy consumption. This drives the industry towards green and sustainable practices.
Implementing these standards has elevated the level of mold making and provided reliable quality assurance for domestic and international clients. A renowned automotive company adheres to these standards when selecting suppliers to ensure that molds meet high requirements, thereby enhancing the quality of automobiles and earning market reputation.
Simultaneously, these standards provide clear directions and guidance for enterprises, enhancing their technological capabilities and management skills, thus boosting product competitiveness and market share. Industry experts emphasize that standards are the soul of the industry, and adhering to them is crucial for enterprises to stand unbeatable in market competition.
The standards and regulations in the Chinese mold making industry play a significant role in driving industry development, improving product quality, and promoting technological innovation. In the future, these standards will continue to be refined and updated, providing a guarantee for the industry’s sustainable development.
5.2 Industry Association and Exhibition Information
The Chinese mold making industry holds a prominent position in the global market, with its technological prowess and industrial scale widely recognized. To promote industry development, the China Mold Making Industry Association regularly organizes exhibitions and exchange activities, providing a platform for showcasing technology, exchanging experiences, and expanding markets. These exhibitions attract numerous domestic and international mold manufacturing enterprises, industry experts, and media.
Take the “China International Mold Exhibition” as an example, which has become the largest and most influential mold industry event in Asia. The number of participating companies steadily increases each year, covering the entire mold manufacturing industry chain. The exhibition showcases advanced equipment, technological achievements, and innovative products, fully demonstrating the strength and vitality of the Chinese mold making industry.
These exhibitions not only provide opportunities for enterprises to showcase their strengths but also serve as a bridge for communication and cooperation. Enterprises can engage in in-depth exchanges with domestic and foreign counterparts, share experiences, discuss technical challenges and market trends, thereby driving industry progress. Moreover, the exhibitions provide opportunities for enterprises to expand their markets, connect with potential global customers and partners, understand market demands and trends, and expand sales channels and partner networks.
An industry expert remarked that participating in these exhibitions enables understanding of the latest industry trends and technological advancements, deep collaboration with peers, and collectively driving industry development. These exhibitions inject new vitality and momentum into the Chinese mold making industry.
5.3 Explanation of Mold Making Related Terminology
Mold making is the core technology of modern industry, involving multiple fields and industries. Understanding the related terminology is crucial in mold making. A mold is a shaping tool for manufacturing industrial products, where precision and durability are key factors determining product quality and production efficiency.
Take automotive parts molds, for example; the manufacturing process requires high precision and complex techniques. A mold may contain dozens or even hundreds of precision components, each requiring strict design and manufacturing. Tolerance is the allowable deviation between actual and theoretical dimensions, critical for the assembly accuracy and performance of automotive parts molds.
Surface roughness is another important term in mold making, affecting mold wear resistance, lifespan, and the final product’s surface quality. Utilizing advanced processing and surface treatment technologies can reduce surface roughness and enhance mold performance.
German engineer Karl Benz once said, “Precision is the soul of industry.” In the field of mold making, a deep understanding and application of related terminology are key to achieving high-precision and high-efficiency manufacturing. The Chinese mold making industry has made significant development achievements and occupies an important position in the global market.
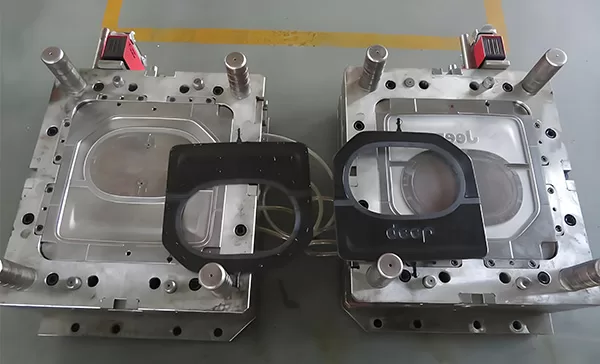
Leave a Reply